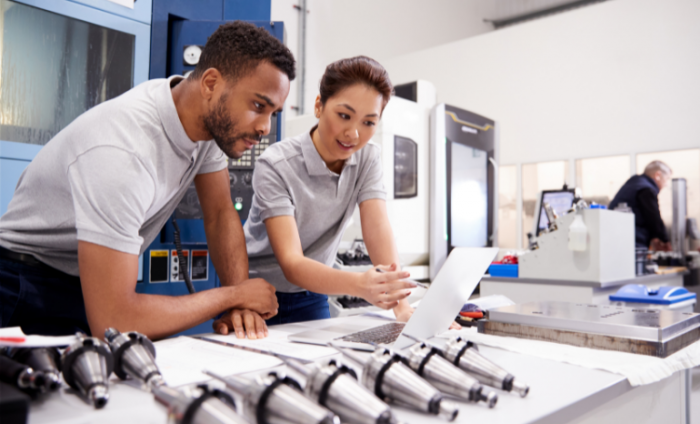
As companies seek to drive returns and increase efficiency, new technologies are the sought-after fix. While this can be an effective option, it can take years to implement and cost millions of pounds, making it inaccessible for most manufacturers. Speaking with The Manufacturer, Bilal Gokpinar explains how his latest research proves the value of frontline employee innovation to increase efficiency within just months.
The article suggests the key to making efficiency gains and increasing ROI is through analysing your customer needs and understanding an organisation in relation to those needs. Research by Bilal and his co-authors, Philipp Cornelius and Fabian Sting, explains the power of frontline employee innovation in this process identifying that up to 75% of all productivity gains can derive from bottom-up employee ideas.
Their research shows for the first time how strategic front-line mobility — the short, focused and purposeful exchange of staff members between different company sites — can substantially boost employees’ contributions to innovation and organisational learning in manufacturing companies.
Fostering a creative culture amongst frontline employees, where they feel their ideas will be taken seriously encourages idea generation, ideas which Bilal says do not have to be ground breaking to effect change and increase the ROI. He explains “improvements can come not by introducing some sophisticated AI, machine learning or industrial automation. Simply let your frontline workers think a bit more.”